Sheet metal is used in a huge number of industries – from automobile and truck (lorry) bodies, aeroplane fuselages and wings, medical tables, to the roofs for buildings – but what exactly is it and how do Engineers use it today?
Sheet Metal’s Role in Machining
Sheet metals are a result of an industrial process involving thinning metal into flat pieces. This one of the basic forms used in metalworking where metal is cut and reshaped into various shapes. Sheet metals have various applications in modern society, with thin metal films called foils, while thicker versions are termed structural steel. There are several objects that are designed using sheet metals, for example, building arches, motor vehicles, and other machines. Sheet metals can be found in two versions, coiled and flat. The coiled sheets are formed from running the metal continuously through roll slitters.
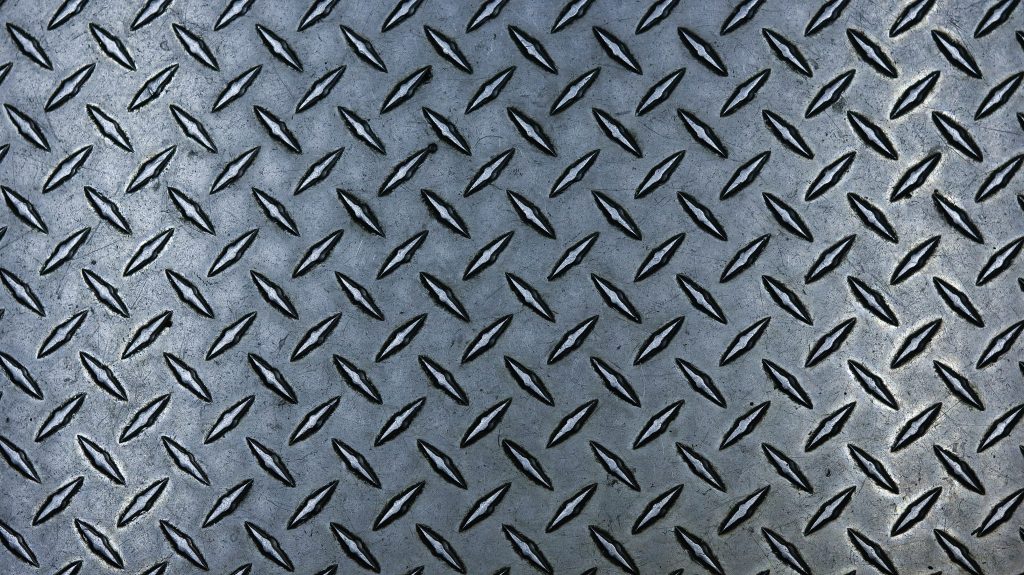
Sheet metals have a standard measurement in millimetres across the globe, unlike in the United States, where they have a non-linear measurement system called gauge. Higher gauge sheets are thinner. Due to the difference in application and malleability, there are different types of metals that can be turned into sheet metals. They include; copper, aluminium, titanium, steel, tin, brass, and nickel. For people going for that class and luxurious look, gold, silver, and platinum can be used to decorate the object.
Sheet metal Applications
This metal form is used in the automobile industry. It is used to build bodies for aeroplanes, cars, boats, and ships.
Iron sheet metals are also used in the energy industry in the making of transformers and other electric machines. This is due to the sheet’s magnetic permeability, also referred to as laminated steel cores.
In ancient times, sheet metals were used in the designing of military armour for the Calvary.
Sheet metals also have endless applications in the construction industry, with the most common use being in designing roofing solutions for buildings. The special sheet metals made of gold, silver, and platinum can be used for decorative features on buildings like arches, doors, and windows.
Sheet metal and Machining
Sheet metal offers a wide range of benefits compared to the common types of metal fabrications and non-metal options. This alternative is fast becoming common among industries due to its cheap nature both in materials purchased as well as the cost of making. In Machining, the process of making sheet metals is cost-effective as you are able to minimize the waste of raw materials. The process ensures the purchase and use of specific material quantities. Leftover materials can be used for other purposes, with shavings being recycled. This overshadows other metal fabrications that involve buying expensive raw materials, with a good portion of the materials being lost in milling to remove unwanted materials.
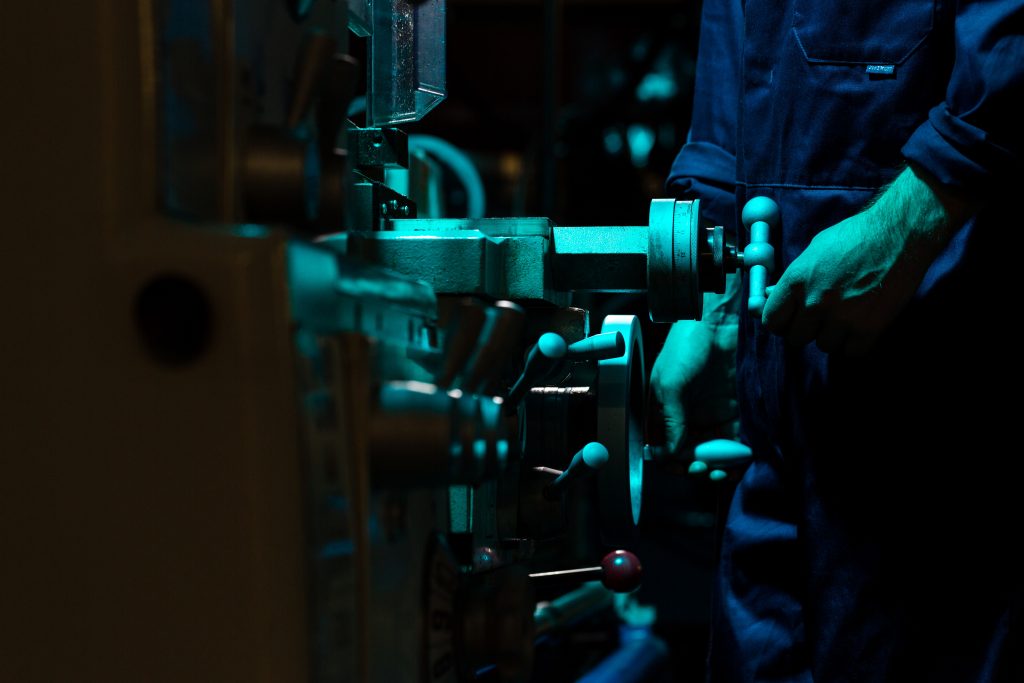
The tech world is constantly coming up with new programs that are designed to ease work. This is seen in new innovative technology like Computer-Aided Design (CAD) that provide programs that make the sheeting process a walk in the park. The program can also design and fabricate the specific shapes formulated within the program at an accurate precision. This program eliminates the hassle of creating a shop design and interpreting the design forming a single platform where the designers can both design, interpret, and come up with a complete fabrication.
In the long-run, implementation of this technology will come in handy when boosting mass production. With an initial expense in setting up production, industries dealing in metal fabrications are set to reap huge returns. Completing the setup allows the spreading of cost over the large pieces produced, reducing production costs and significantly eliminating processes like Machining.
Fabrication Techniques for Sheet Metals
- Shearing- Shearing is probably the oldest style of cutting sheet metal.
- Punch Press- This method uses a punch and dies that make holes and other shapes and designs. This method is both efficient and economical in cutting simple designs. Operating at hundreds of strokes per minute, this technique becomes reliable in processing parts faster.
- Laser Cutting – This method employs the use of gases like nitrogen, helium, oxygen, and carbon dioxide to burn away material producing a clean edge.
- Photochemical Machining – This is where modern technology earns its stripes. This technique involves using a CAD program to control the etching process to leave a pattern chemically activated to emit unwanted material.
- Hemming- Hemming is where metal edges are folded over themselves or over another sheet metal to obtain stronger rounded edges. This technique is useful in improving the outlook and strength of the metal. Hemming has two processes with different applications; roll hemming and conventional die hemming. Roll hemming is done using a hemming roller with a robot guiding the roller to form a flange. Conventional hemming die involves folding the flange over the entire sheet using a hemming tool.
Sheet metals can be manipulated to fit different shapes and sizes that have multiple applications across industries. Even the medical field benefits from sheet metals as they are used for manufacturing metal tables as well as other medical devices