The Indian Space Research Organisation (ISRO) has recently made significant strides in additive manufacturing, specifically in the production of rocket engines. On May 9, 2024, ISRO successfully conducted a hot-fire test of a 3D-printed liquid-fueled rocket engine, marking a breakthrough that could revolutionize India’s space program and align it with global trends in space exploration.
ISRO’s Successful Hot-Fire Test
The hot-fire test, performed at the ISRO Propulsion Complex in Mahendragiri, involved the PS4 engine used in the fourth stage of India’s Polar Satellite Launch Vehicle (PSLV). The engine, manufactured using laser powder bed fusion (LPBF) technology, burned a hypergolic mixture of nitrogen tetroxide and monomethyl hydrazine for 665 seconds. This achievement validates the performance and reliability of the 3D-printed engine.
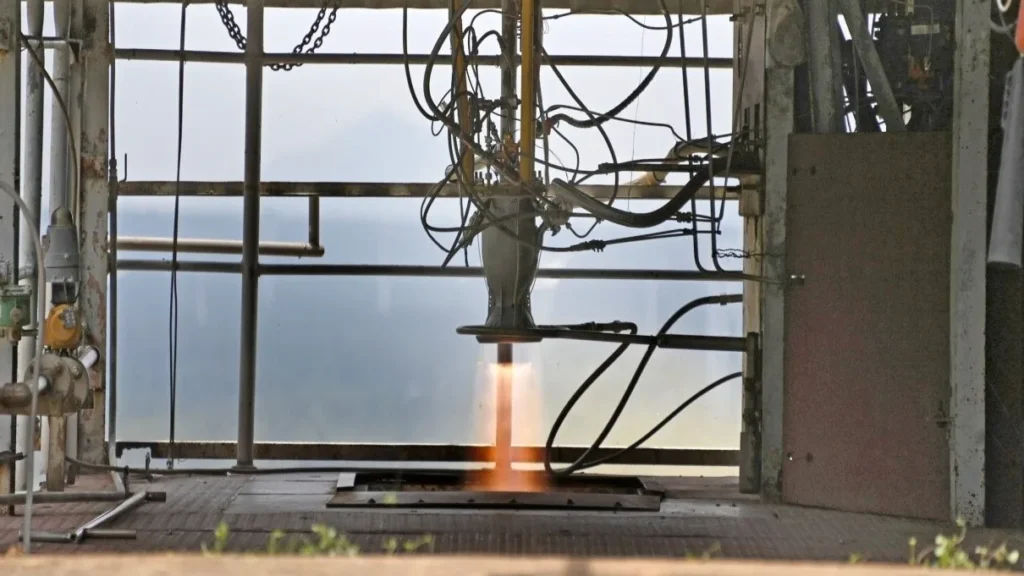
Adopting additive manufacturing techniques has brought about significant improvements in the production of the PS4 engine. By utilizing LPBF technology, ISRO has reduced the number of engine parts from 14 to a single piece, eliminating 19 weld joints in the process. This streamlined design has resulted in substantial savings in raw material usage, with the 3D printing process requiring only 30.2 pounds (13.7 kilograms) of metal powder compared to the 1,245 pounds (565 kilograms) of forgings and sheets needed in conventional manufacturing. Additionally, the overall production time has been reduced by an impressive 60%.
ISRO’s success in 3D printing the PS4 engine was made possible through a collaboration with Wipro 3D, a division of Wipro Infrastructure Engineering and a leader in additive manufacturing services in India.
Wipro 3D was crucial in redesigning the engine to ensure compatibility with Design for Additive Manufacturing (DfAM) principles. The company utilized advanced 3D printing machines from various leading brands to manufacture the engine, highlighting the importance of industry partnerships in advancing space technology.
Before the successful 665-second hot-fire test, ISRO conducted rigorous evaluations to ensure the reliability and performance of the 3D-printed PS4 engine. The injector head underwent separate testing, and detailed simulations were performed to validate the engine’s design. Four shorter tests, totalling 74 seconds, were also conducted to assess the engine’s performance. The final long-duration test confirmed that the engine met all expectations, exhibiting stable thrust and chamber pressure throughout the firing.
The successful integration of the 3D-printed PS4 engine into the PSLV program is a significant milestone for India’s space endeavours. The PSLV, a workhorse launch vehicle capable of delivering payloads of up to 3,860 pounds (1,750 kilograms) to sun-synchronous polar orbits, will now benefit from the enhanced efficiency and reduced production time offered by additive manufacturing. This breakthrough not only opens up possibilities for ISRO to explore the use of 3D printing in other projects but also positions India as a potential leader in the democratization of space technology. This achievement paves the way for future advancements and empowers India’s ambitious space endeavours.
India’s 3D-printed rocket engine test is a significant milestone in the country’s space program. By embracing additive manufacturing technology, ISRO has demonstrated its commitment to sustainable and efficient space exploration. This breakthrough not only aligns India with global trends in the space sector but also showcases the nation’s potential to become a leading player in the democratization of space technology. As ISRO continues to push the boundaries of innovation, the successful implementation of 3D printing in rocket engine production will undoubtedly pave the way for future advancements and empower India’s ambitious space endeavours.
TL;DR:
- ISRO successfully tested a 3D-printed liquid-fueled rocket engine on May 9, 2024
- The PS4 engine used in the PSLV rocket was manufactured using laser powder bed fusion technology
- 3D printing reduced engine parts, eliminated weld joints, and saved raw materials and production time
- Wipro 3D collaborated with ISRO to redesign the engine for additive manufacturing compatibility
- Rigorous testing, including a 665-second hot-fire test, validated the engine’s performance and reliability
- The breakthrough aligns India with global trends in space exploration and democratization of the sector