A team of international researchers led by Pennsylvania State University has developed a new type of ferroelectric polymer that could potentially be used as ‘artificial muscles’ in advanced robotics and medical devices.
This innovative material can convert electrical energy into a mechanical strain more efficiently than previous methods, overcoming the limitations of traditional piezoelectric polymer composites.
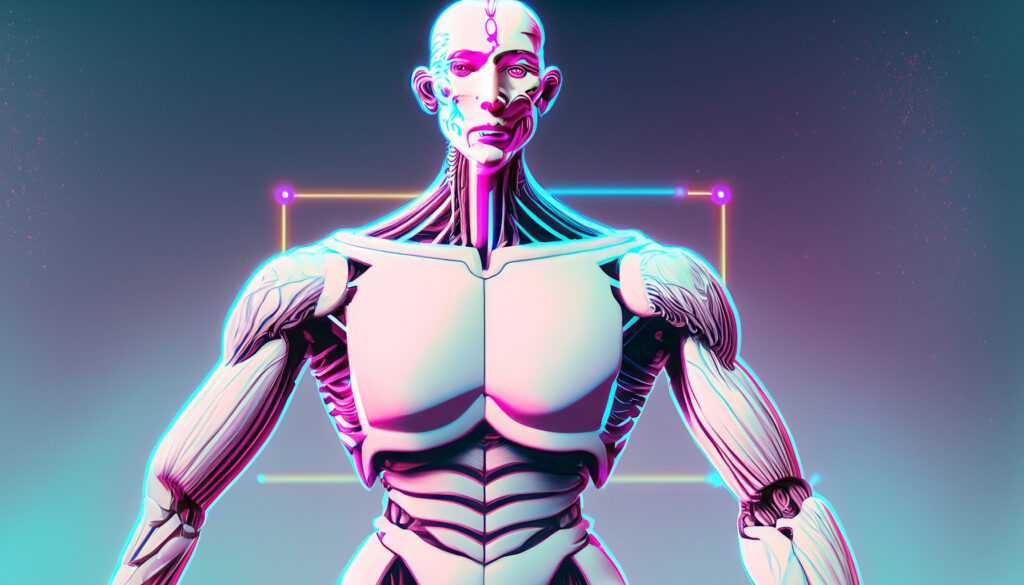
The new ferroelectric polymer is a promising development for soft actuators, which are materials that change shape when an external force is applied. Unlike rigid actuators, soft actuators offer strength, power, and flexibility, making them extremely useful in robotics.
The researchers have demonstrated that by incorporating nanoparticles into a type of polymer, polyvinylidene fluoride, they could create an interconnected network of poles within the polymer. This network induced a ferroelectric phase transition at much lower electric fields than required. This was achieved via an electro-thermal method using Joule heating, which occurs when the electric current passes through a conductor and produces heat.
However, there are still challenges to overcome before these ‘artificial muscles’ become a reality. The force of soft materials needs to be improved, and a ferroelectric polymer actuator typically requires a very high driving field. The researchers are optimistic that their new approach can address these challenges and open up new possibilities for medical devices, optical devices, and soft robotics applications.
TL;DR:
- Researchers have developed a new type of ferroelectric polymer that could be used as ‘artificial muscles’ in advanced robotics and medical devices.
- The new material can convert electrical energy into a mechanical strain more efficiently than previous methods.
- The researchers used an electro-thermal Joule heating method to induce a ferroelectric phase transition at much lower electric fields.
Published as “Electro-thermal actuation in percolative ferroelectric polymer nanocomposites” in Nature Materials volume 22, pages873–879 (2023)