Tata Steel UK and JCB have signed a Memorandum of Understanding (MoU) to supply low-CO2 “green” steel, a significant step towards decarbonisation.
The landmark agreement marks Tata Steel UK’s first supply deal since announcing its £1.25 billion joint investment with the UK government to transition to high-quality, low-CO2 steel production in South Wales.
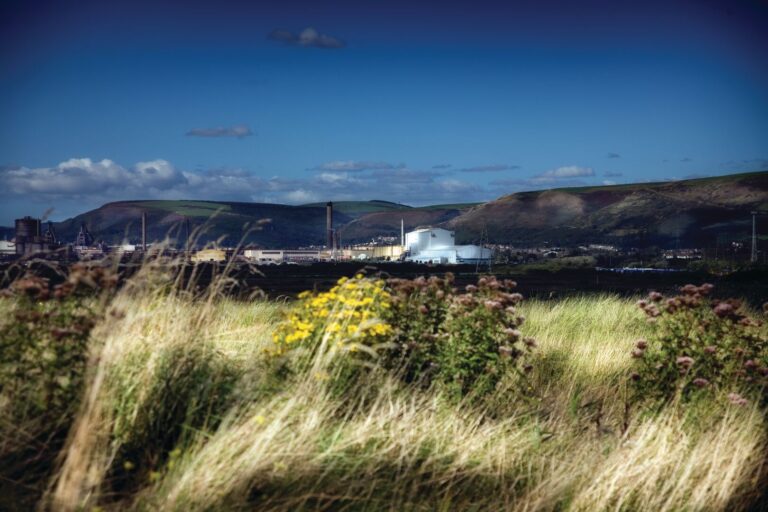
Tata Steel’s ambitious transformation plans involve the construction of a state-of-the-art Electric Arc Furnace (EAF) at its Port Talbot site. With a capacity of 3 million tonnes per year, this EAF will be one of the largest in the world, offering a more environmentally friendly alternative to the traditional blast furnace method.
The EAF technology leverages UK-sourced scrap metal, eliminating the need to import millions of tonnes of iron ore and coal. Tata Steel aims to reduce the site’s CO2 emissions by up to 90%, contributing to a 1.5% decrease in the UK’s overall carbon emissions.
What is an Electric Arc Furnace (EAF)
An Electric Arc Furnace (EAF) is a high-temperature furnace that uses electric arcs to melt and refine steel scrap and other ferrous materials to produce new steel.
Unlike traditional blast furnaces, which rely on coal and iron ore as raw materials, EAFs primarily use recycled steel scrap, making them a more environmentally friendly option for steel production.
How does an Electric Arc Furnace work?
The process of steel production in an EAF can be broken down into several key steps:
- Charging: The first step is to load the furnace with steel scrap and other ferrous materials, such as direct reduced iron (DRI) or hot briquette iron (HBI). This is typically done using a large basket or a conveyor system. The scrap can come from various sources, including old vehicles, appliances, and construction materials.
- Melting: Once the furnace is charged, electrodes are lowered into the scrap pile. These graphite electrodes can be up to 2 meters in diameter and 10 meters in length. A high-voltage electric current is passed through the electrodes, creating an electric arc between the electrode tips and the scrap. The heat generated by the electric arc can reach temperatures of up to 1,800°C (3,272°F), sufficient to melt the scrap and create a molten steel pool.
- Refining: As the scrap melts, impurities such as silicon, phosphorus, and sulfur are removed from the steel through refining. This is done by adding various fluxes, such as lime and dolomite, to the molten steel. These fluxes react with the impurities, forming slag that floats on the molten steel and can be removed. Oxygen is also injected into the furnace to remove carbon and other unwanted elements.
- Alloying: Once the steel has been refined, alloying elements such as nickel, chromium, or manganese can be added to the molten steel to achieve the desired steel grade and properties. These elements are typically added as ferroalloys, pre-mixed iron combinations and alloying elements.
- Tapping: After the steel has been refined and alloyed, it is ready to be tapped from the furnace. This is done by tilting the furnace and allowing the molten steel to flow through a taphole into a ladle. The slag, which has a lower density than the steel, is left behind in the furnace and can be tapped separately.
- Casting: The molten steel in the ladle is then transported to a continuous casting machine, where it is poured into a mould and solidified into semi-finished steel products such as blooms, billets, or slabs. These products can then be further processed into finished steel products such as beams, bars, or sheets.
Advantages of EAFs
EAFs offer several advantages over traditional blast furnaces:
- Flexibility: EAFs can produce a wide range of steel grades by adjusting the composition of the scrap and the alloying elements added during the refining process. This flexibility allows steelmakers to respond quickly to changes in market demand.
- Energy efficiency: EAFs are more energy-efficient than blast furnaces, as they use electricity rather than coal to melt the scrap. This reduces energy consumption and allows for the use of renewable energy sources such as solar or wind power.
- Lower environmental impact: By using recycled steel scrap as the primary raw material, EAFs reduce the need for mining and processing virgin iron ore, which can have significant ecological consequences. Compared to blast furnaces, EAFs also emit fewer greenhouse gases and other pollutants.
- Smaller footprint: EAFs are typically smaller and more compact than blast furnaces, making them more suitable for urban or space-constrained locations.
As the global steel industry faces increasing pressure to reduce its environmental impact and carbon footprint, EAFs are expected to play an increasingly important role in steel production. Many steelmakers are investing in new EAF capacity and upgrading existing facilities to improve efficiency and reduce emissions.
One promising development is using direct reduced iron (DRI) as a feedstock for EAFs. DRI is produced by reducing iron ore using natural gas or hydrogen instead of coal, resulting in a lower-carbon alternative to traditional blast furnace iron. By combining DRI with renewable electricity, EAFs have the potential to produce “green steel” with a significantly lower carbon footprint.
As part of the new agreement, JCB will integrate the green steel supplied by Tata Steel into its machinery range. This aligns with JCB’s ongoing commitment to carbon reduction in its manufacturing processes and equipment. JCB has been at the forefront of decarbonisation in the construction industry, launching its “Road to Zero” programme in 2010.
Over the years, JCB has achieved notable industry milestones, such as developing the first-ever electric mini-digger in 2018 and creating the first hydrogen-powered machine in 2021. The company continues to expand its range of fully electric-powered equipment and is currently testing the world’s first construction machines powered by hydrogen combustion engines.
The History of Steel at Port Talbot
Port Talbot, a coastal town in South Wales, has been synonymous with steel production for over a century. The town’s journey from a small village to a global steel hub is a fascinating tale of industrial growth, technological advancements, and the resilience of its community.
The origins of steel production in Port Talbot can be traced back to the early 20th century. In 1901, the Gilbertson family, who owned a tinplate works in the nearby village of Pontardawe, purchased land in Port Talbot to build a new steelworks. The site was chosen for its strategic location, with access to deep-water ports that could accommodate large ships carrying raw materials and finished products.
Construction of the Port Talbot steelworks began in 1902, and the first blast furnace was lit in 1905. The initial production capacity was modest, with the plant producing around 150,000 tons of steel annually. However, the steel demand skyrocketed, fueled by the expansion of railways, shipbuilding, and other industries.
Over the next few decades, the Port Talbot steelworks underwent significant expansions and modernisations to keep pace with the increasing demand for steel. In the 1920s, Baldwins Ltd., a substantial steel producer in the UK, acquired the plant. Under new ownership, the works continued to grow, with additional blast furnaces and rolling mills being built.
One of the most significant milestones in the history of the Port Talbot steelworks came in the 1950s with the construction of the Abbey Works. This new facility, named after the nearby Margam Abbey, was built to accommodate the latest technological advancements in steel production. The Abbey Works featured a state-of-the-art strip mill, which enabled the production of higher-quality steel at a faster rate.
The 1960s and 1970s saw further expansions and upgrades at the Port Talbot steelworks. The plant’s capacity increased to over 3 million tons of steel annually, making it one of the largest steel producers in Europe. The works also diversified its product range, producing steel for various applications, including automotive, construction, and household appliances.
The steel industry in the UK faced significant challenges in the last half of the 20th century, and Port Talbot was not immune to these difficulties. The global oil crisis of the 1970s led to a downturn in demand for steel, resulting in job losses and reduced production at the plant. The 1980s brought further challenges, with increased competition from cheaper imported steel and a decline in the UK’s manufacturing sector.
Despite these challenges, the Port Talbot steelworks demonstrated remarkable resilience. In the 1990s, the plant was acquired by Corus, a merger between British Steel and the Dutch company Hoogovens. Under Corus, the works underwent further modernisation, with investments in new technologies and processes to improve efficiency and reduce environmental impact.
In 2007, Corus was acquired by Tata Steel, an Indian multinational steel-making company. Tata Steel’s acquisition brought new opportunities for the Port Talbot steelworks, with access to global markets and resources. However, the plant continued to face challenges, including the global financial crisis 2008 and increasing pressure to reduce carbon emissions.
Today, the Port Talbot steelworks remains a vital part of the UK’s steel industry, employing thousands of people and producing high-quality steel for various applications. However, the plant faces new challenges, such as climate change and the need to decarbonise the steel industry.
Tata Steel’s recent announcement of a £1.25 billion investment in the Port Talbot steelworks, including constructing a new Electric Arc Furnace (EAF), marks a significant step towards a more sustainable future for steel production in the town. The EAF technology will enable the plant to produce steel using recycled scrap metal, reducing its reliance on coal and iron ore and cutting carbon emissions by up to 90%.
This investment secures the future of steel production in Port Talbot and positions the town at the forefront of the green industrial revolution. By embracing new technologies and adapting to the challenges of the 21st century, Port Talbot continues to demonstrate the resilience and innovation that have characterised its steel industry for over a century.
The history of steel in Port Talbot is a story of industrial might, technological progress, and the enduring spirit of a community that has weathered many storms. As the town embarks on a new chapter in its steel-making journey, it does so with a proud legacy behind it and a bright, sustainable future ahead.
The partnership between Tata Steel and JCB represents a significant milestone in the UK’s transition towards a circular economy. By collaborating to create a low-carbon supply chain, these two major manufacturers are setting an example for other industries to follow. The integration of green steel into JCB’s machinery range has the potential to drive sustainability across the construction sector and encourage other companies to adopt similar practices.
The £1.25 billion investment, which includes a UK government grant of up to £500 million, is the most significant capital expenditure in UK steel production for decades. This investment underscores Tata Steel’s commitment to transforming Port Talbot into one of Europe’s premier centres for green steel-making. By sourcing 75% of the required raw materials from within the UK, up from the current 10%, Tata Steel aims to enhance the country’s self-sufficiency in steel production and increase resilience to global supply chain disruptions.
The green steel deal between Tata Steel and JCB represents a significant step in decarbonising the steel and construction industries and the partnership has the potential to drive meaningful change and contribute to the UK’s net-zero ambitions.
TLDR
- Tata Steel UK and JCB signed an agreement to supply “green” steel, following Tata’s £1.25 billion joint investment with the UK government
- Tata Steel will build one of the world’s largest Electric Arc Furnaces at Port Talbot, capable of producing 3 million tonnes of steel annually while reducing CO2 emissions by up to 90%
- The new furnace will use UK-sourced scrap metal instead of imported iron ore and coal, increasing domestic raw material usage from 10% to 75%
- JCB will incorporate this low-CO2 steel into their machinery, aligning with their existing environmental initiatives which include electric and hydrogen-powered construction equipment